The construction industry is one of the biggest producers of carbon, so it is beholden on companies in the sector to look at ways of reducing our carbon emissions.
As Head of Supply Development at Balfour Beatty, I am constantly consuming information about how the world is changing, and not necessarily always for the better.
I cannot ignore the evidence of the climate crisis any longer as every other month catastrophic events seem to befall our planet, which makes me motivated to act. As a large construction business, I recognise our potential impact and moral responsibility to act and educate the industry along the way.
Securing Fife College
When Balfour Beatty was awarded the contract to build Fife’s College’s new Learning Campus, an innovative 20,000m2 site in Dunfermline, I knew this was an opportunity to build collaboration into the project from the very start, in fact even before a single shovel had hit the ground.
The Learning Campus is Scotland’s first net zero college and a pathfinder example for the Scottish Government’s Net Zero Public Sector Buildings (NZPSB) standard. To help meet those exacting requirements, Balfour Beatty held a workshop for 60 of the project’s key suppliers, which was sponsored by Zero Waste Scotland, a not-for-profit organisation funded by the Scottish Government.
We wanted to create an environment where companies in the supply chain could share ideas and collaborate on ways of reducing carbon during construction of the Campus and its subsequent operation. One of the initiatives presented was a new packaging concept being developed by Whitecroft Lighting that would drastically reduce traditional packaging waste and eliminate single use packaging for its products.
The Packaging Problem
Whitecroft estimated that less than 50% of its cardboard packaging material was being recycled after its products had been delivered, due to external packaging getting wet or not being recycled properly, as well as the amount of plastic wrapping that could not be recycled.
To address this issue Whitecroft had been working with the Cardiff Metropolitan University and consultants PDR on a new modular packaging concept called Geopak™ that would not only be reusable and recyclable, minimising waste, it would bring additional benefits in the form of efficient transportation of lighting products and the installation contractor being able to track them onsite after delivery via GPS tagging.
At Balfour Beatty we had no knowledge of the challenges Whitecroft faced during the manufacture and packaging of its products, while Whitecroft had little understanding of how its products were handled once they arrived on a construction site. Working closely with Whitecroft, PDR and Cardiff Metropolitan University, we mapped out each step of the journey for its lighting products, from manufacture to packaging, and transportation through to installation.
By collaborating we planned a process and created a solution that addressed all the practical needs of each stakeholder, but ultimately would help to reduce the carbon footprint of the Learning Campus development. By working together, I am proud to say that Fife College project was the first time Geopak™ was used commercially.
The Geopak™ Solution
The simplicity of the Geopak™ concept is that by using a standardised “tote” module that will accommodate up to 90% of Whitecroft’s range, products can be packed efficiently, minimising wasted space and unnecessary packaging. Because the crates are made from recycled polypropylene and can be reused at least 12 times, as well as being recycled at the end of life, this is massive saving in wasted material and carbon emissions.
The bigger pallet boxes into which the smaller totes are packed eliminate the need for single use plastic wrapping. When the Geopak™ totes have been emptied they can be folded down and stored in the flat packed pallet boxes onsite until collected by Whitecroft for reuse on another project. This provides maximum utilisation of space both onsite and when being transported back to Whitecroft.
But with its Geopak™ innovation, Whitecroft is looking beyond straightforward recycling and elimination of packaging waste by creating a packaging solution that can be repurposed and embrace the circularity approach at the heart of Whitecroft’s environmental philosophy.
To this end, each piece of Geopak™ packaging features an GPS enabled tag which means the packaging and lighting products can be tracked onsite using geofencing to an accuracy of two to three metres, enabling deliveries to be logged when they arrive, and ensuring that valuable assets can be tracked when they are moved onsite.
Anyone onsite can access the geotagging information in seconds and have full visibility of the assets at any stage of the project. The tags also enable the quick location of the flat packed empty Geopak™ packaging when they are ready for collection.
Closing the Circularity Loop
We estimate that two tonnes of packaging waste will be eliminated over the life of the Campus project alone using Geopak™, while the reduction in waste management will save on average £6,000 per site, as well as the associated benefit in reduced carbon. Whitecroft plans to implement Geopak™ in all its major projects over the next two years, taking the equivalent of 100,000 cardboard cartons and the associated carbon out of the supply chain.
What is particularly inspiring about working on the Geopak™ project with Whitecroft is that it is not just about recycling or reusing packaging material, or even striving to meet a stretching Net Zero carbon target, for that matter. It's about rethinking and reimagining our processes and innovating right from the design stage to the manufacturing of materials, through to the construction.
This approach will result in a significant reduction of waste for the Fife College project, which will increase as the packaging is reused again on future Whitecroft projects. With Geopak™, Whitecroft is creating a circular model that also meets the business needs of the company and its customers, saving waste, reducing the amount of packaging being manufactured, and improving efficiency on the construction site, benefits that will only increase as Geopak™ is rolled out to more customers and projects.
By working with Balfour Beatty on the Fife College project, it also sets the standard for innovation and collaboration in the construction industry, which is vital for everyone in the supply chain.
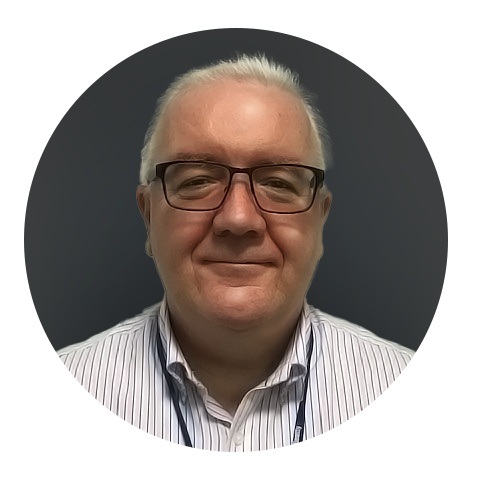
Net-zero carbon, the circular economy and digitalisation will be key drivers in the future, not only to help us survive, but also thrive in this decisive decade.
Jim Brannan is the Head of Supply Chain Development at Balfour Beatty.